Galvanic corrosion with expansion bolt
Galvanic corrosion at expansion bolt is probably one of the greatest safety risks on climbing routes. It is often referred to as contact corrosion or bimetallic corrosion . It has a negative impact on the breaking load of the affected components.
We therefore want to provide comprehensive information on this topic.
Firstly, about the principle of this type of corrosion. Secondly, we present practical examples. And thirdly, we give you simple tips on how to prevent it.
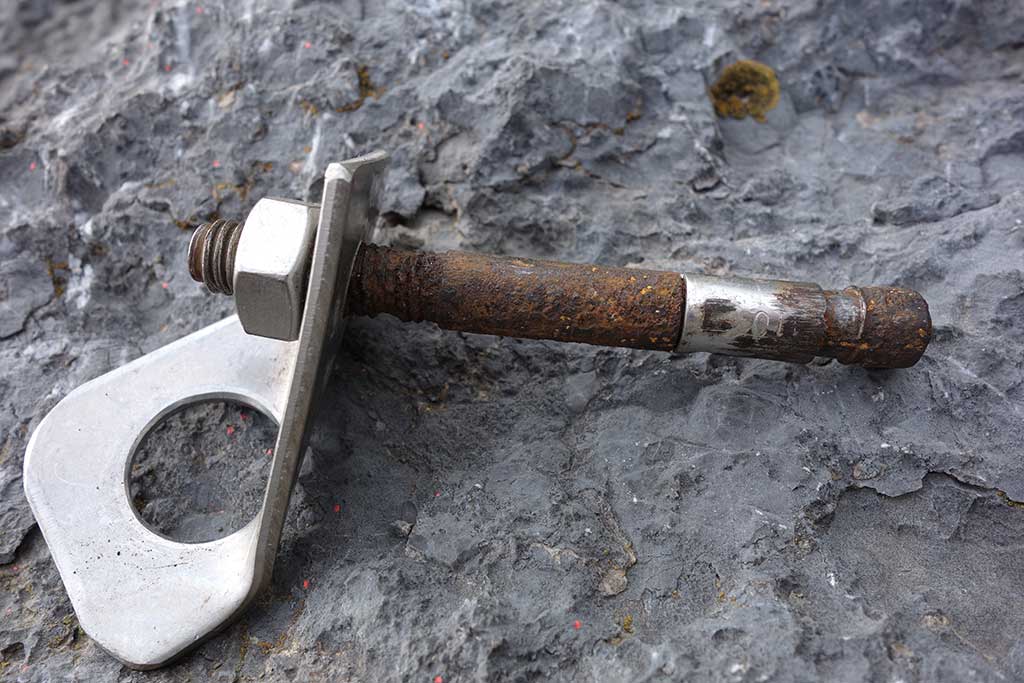
Galvanic corrosion principle
In simple terms, galvanic corrosion occurs at expansion bolt for the following reason. Components with different precious metals have been processed. E.g. a zinc plated expansion bolt with a stainless steel bracket.
The influence of water then causes electrons to migrate. From base metal to noble metal . In the process, the base metal is decomposed (“oxidized”). To stay with our example. The zinc plated expansion bolt (= base metal) begins to “rust”.
The precious metal, the positively charged cathode, is “reduced” in the process.
This happens mainly just behind the bolt hanger in the drilling hole. This is because water can accumulate perfectly between the thread and the rock. It then acts as a so-called “electrolyte”. In other words, as a liquid through which the electrons can flow.
This chemical process – which in simple terms works like a small battery – can therefore progress unhindered. Over the years, the breaking load of the base component steadily decreases and eventually becomes a danger. This is because the maximum breaking load values are significantly undercut.
Estates and Rapid limbs also affected
Unfortunately, galvanic corrosion at expansion bolt very often also affects the lower off / climbing anchors. Here, a stainless steel lower off was/is classically mounted on zinc plated expansion bolt.
Please also note. Bimetal corrosion will also occur if you attach a zinc plated screw link-Rapid link to a stainless steel bolt hanger or vice versa!
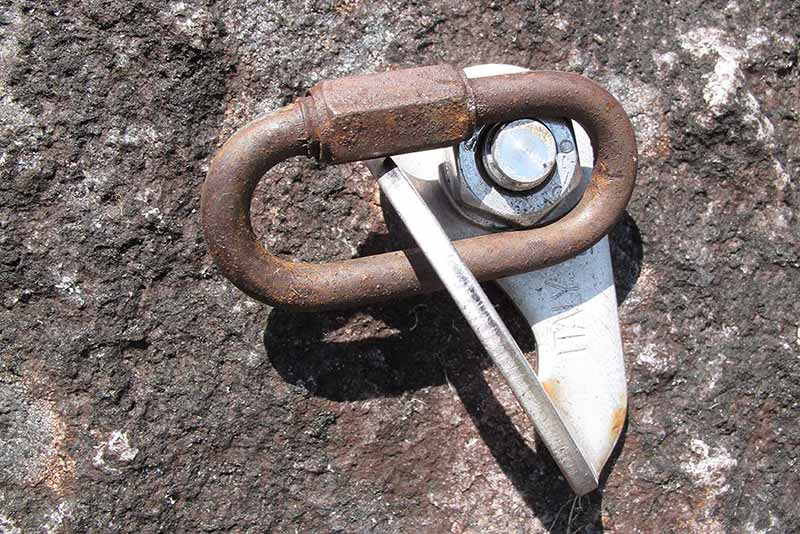
With glue in bolt there can be no contact corrosion. This is because a glue in bolt consists of only one type of metal!
Stronger corrosion in “salty” environments
In simple terms, contact corrosion at expansion bolt depends on the following factors:
– Salt content of the “electrolyte”: The more “aggressive” the water, the stronger the reaction of the two different metals.
– Ambient temperature: In the range of 25°-35° C, salt water offers the best solubility for many salts and leads to accelerated corrosion in this temperature range.
Consequently, the degree of galvanic corrosion can vary greatly at expansion bolt. On a shady and dry granite rock, it will be rather low. On a damp and sunny limestone rock, it will be rather high.
The individual processes are explained in detail at the bottom of the article!
Click here for the article on galvanic corrosion / contact corrosion on Wikipedia.
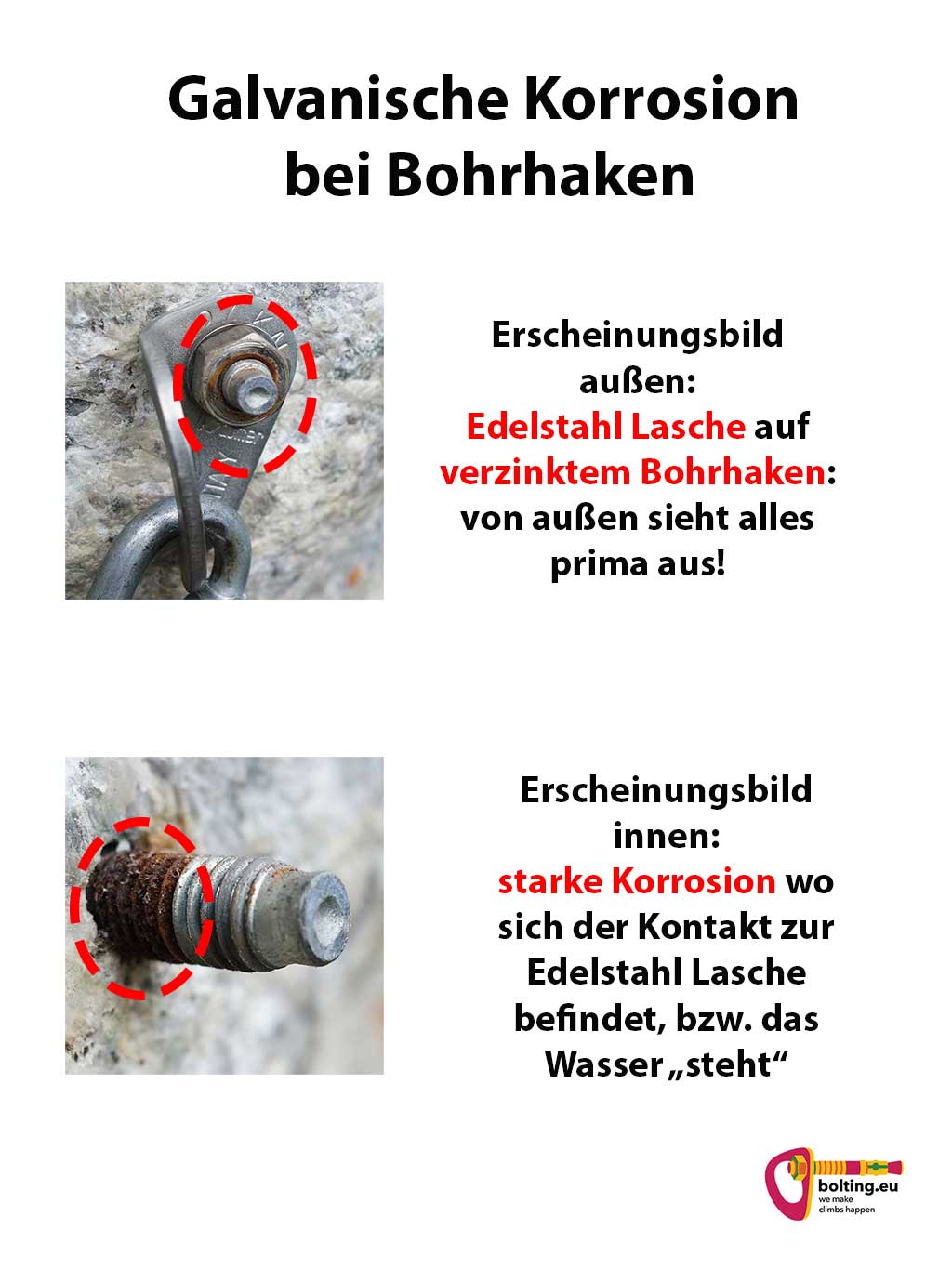
Practical causes of galvanic corrosion
There are many practical reasons for processing components made of different metals. In the following, we would like to present the three most important causes from our point of view:
- lack of awareness / know-how: many developers are simply not aware of the principle of contact corrosion at expansion bolt. In short: they process components of varying quality when bolting without realizing what this entails.
- Incorrect storage: How to store? Yes, exactly, storage! Often the “sloppy” throwing together of the expansion bolt, bolt hangernuts and washers during storage is often the cause of bi-metal corrosion. Once zinc plated and stainless steel components have been mixed up in the “drilling box”, incorrect assembly is quite likely.
- Tabs that have fallen off: Every climber knows the situation. You get on a route and suddenly the bolt hanger is missing somewhere! Then someone replaces the bolt, the washer and the fixing nut. Very often, components with a different steel quality are added.
Avoidance of contact corrosion
This prevents galvanic corrosion at expansion bolt.
Firstly, zinc-plated expansion bolt or galvanized bolt hanger should be avoided altogether if possible.
Climbing area owners should not even ask themselves this question when building a climbing area. Due to the amendment to EN standard 959, they now have to use stainless steel components anyway. This means that there should no longer be any problems with new developments. In other words, it is a clear plea for rapid climbing area rebolting in order to minimize legal risks.
For developers who are financing new buildings out of their own pockets, the use of zinc-plated steel, which is much cheaper, is only too understandable. Secondly, if zinc plated components are used, everything should be made of galvanized steel. I.e. expansion bolt and the lug.
Of course, the same applies here. If possible, use stainless steel components because they simply last much longer!
Thirdly. Be very careful when storing your bolting hardware. Do not mix up stainless steel and zinc plated steel components. It is best to have a small box for both zinc plated and stainless steel material. This will help you avoid this classic mistake when bolting a climbing route with expansion bolt!
Fourthly, we need to do the appropriate educational work to increase bolting know-how in the community. To come back to the example of the missing tab. This is the only way to prevent any tabs from being screwed on without thinking.
You can find more technical articles from us on the bolting blog!
“Due to the amendment to EN standard 959, climbing areas in Haltern are obliged to use stainless steel products anyway.”
Climbing area check
Bolting.eu offers a climbing area check as part of its services. We put all desired climbing routes and sectors through their paces.
In addition to other criteria, we also look for galvanic corrosion at expansion bolt.
We also carry out representative pull-out tests and can make a statement about the condition of the protection.
Detailed explanations
“Corrosion” comes from the Latin “corrodere” and means “to eat away” or “to decompose”. In chemistry, corrosion therefore means the decomposition of a substance. This occurs through the reaction of a mostly metallic component with other components from its environment. This requires a substance that “binds” the two reaction elements together. A so-called corrosion element. Water with dissolved salts (“electrolyte”), for example, is a perfect example.
The following picture illustrates the principle. The expansion bolt is made of base metal, zinc plated steel. The bolt hanger and the fastening nut are made of stainless steel. The two different metals represent the reaction partners. The corrosion element is water. It collects in the drilling hole behind the bolt hanger on the threaded shank. This is why corrosion is greatest here.
This type of corrosion describes the decomposition of two metals of different nobility. They react with each other with the help of a “conductive” liquid (“electrolyte”).
The metals act like electrodes. These are differently charged poles that want to equalize their voltage difference. They therefore exchange electrons via the “conductive” liquid. Put simply, this creates a “current flow”.
In simple terms, it works like this:
The electrons from the atoms of the less noble metal first migrate via the “conductive” liquid into the more noble metal.
This means that atoms with “too few” electrons remain in the less noble metal. These are therefore referred to as negatively charged ions. Consequently, the base metal becomes the negatively charged pole (anode).
In the noble metal, the electrons are absorbed from the “conductive” liquid. As a result, these metal atoms suddenly have one electron too many. They therefore become “positively” charged ions. Consequently, the noble metal becomes the positive pole (cathode).
The two poles now try to equalize their voltage difference via the conductive liquid. This means that the electrons begin to flow in a circle. A closed circuit is created.
However, the potentials are never completely equalized. The base metal gives off more electrons than it gets back. Oxidation” creates a stable compound again. However, this destroys the metal over time. In other words, it “rusts”.
As a result, the precious metal absorbs more electrons than it emits. It is “reduced and thus protected.
Firstly, at least one of the components of the fixed point must be made of a different metal. As a rule, we are talking about zinc plated steel here. This can be the expansion bolt itself and/or the bolt hanger, washer and fastening nut.
Secondly, it also needs water and time.
The three classic combinations for the incorrect mixing of dissimilar metals are.
1) expansion bolt (+ washer + nut) made of zinc-plated steel and the bolt hanger made of stainless steel
2) Bolt hanger made of zinc plated steel and the expansion bolt (+ washer + nut) made of stainless steel
3) Mix-mash of zinc plated steel and stainless steel components
The water required for galvanic corrosion at expansion bolt simply comes from rain or humidity.
It remains perfectly suspended between the individual components in the drilling hole. There it acts as a “conductive” liquid (“electrolyte”) between the two different metals. They represent differently charged poles that want to equalize their voltage potential.
To do this, the electrons migrate from the zinc-plated steel via the water to the stainless steel. Then on to the electrolyte. Finally, they return to the zinc-plated steel. The electrons begin to “flow. In other words, a closed circuit is created.
The base metal (- pole) becomes the so-called “reducing agent”. The zinc-plated steel is ultimately oxidized and “eaten up”.
The stainless steel (+ pole), on the other hand, becomes an “oxidizing agent”. The steel is protected by the reaction.